Cleaning in Place System
The Cleaning in Place System is designed to organize the washing and disinfection of the fillers and all the pipes used in the bottling lines.
Before the CIP came on-line the filler was cleaned manually, thereby requiring the allocation of manual labour. The washing of the bottles, which happens before the filling, also meant the wastage of a great deal of water given that all the water used to wash the bottles was disposed of. In addition to the greater consumption of water, these operations demanded a greater consumption of energy.
Initially, CIP was installed to perform the washing of the filler of one of our automatic bottling lines, which became fully functional in May 2017.
CIP – Washing and disinfection of the bottling lines
Hot water is used for the washes during the week, and detergent is now no longer used. Every Friday, hot water and detergent are used in order to maintain hygiene levels during the longer stoppage times over the weekends.
We have reduced the number of employees from 3 to 2 and use up to 1800 litres of water a day instead of the 6000 litres we used before having this equipment.
CIP – Water recirculation in the rinser
CIP has installed a water filtration unit to rinse the bottles, with a tank which recirculates the water, allowing it to be reused after sterilization.
This closed system allows an important economisation of water consumption and results in only 300 litres per day being used.
Heat Exchanger
After CIP was set up, and as an additional measure, a heat exchanger was installed, which allows the capture and reuse of the thermal energy of the water used in the washing. This energy is used for the preheating of the next wash cycle.
The heat exchanger operates at a temperature of 85ºC, which is sufficient to sterilise the water. This heat exchanger makes it possible to have a sterilised wash in just three phases: cold water – hot (85ºC) water – cold water. Washing and sanitising with detergent is done with cold water but in five phases: water – detergent – water – detergent – water.
The heat exchanger provides a dramatic reduction in energy (gas) used for heating the water for washing. Gas consumption has been reduced by 75% in value, in other words the current gas cost is 25% of what it was before the CIP equipment was installed.
Results:
This machinery allows for several savings during and at the end of the filling process, both in terms of the act of filling and in the cleaning and disinfection of the line and tubes:
• Detergent use reduced by 80%. We have eliminated all use of detergents during the week, using only hot water
• Reduction of water consumption during the bottle wash procedure
• Reduction of water consumption for washing the fillers, pipes and hoses
• Reduction of the energy consumption associated with the washing procedures
• We have raised the level of quality and washing to an internationally recognized standard
We shall extend the CIP to the fillers of the other two automatic bottling lines In 2019.
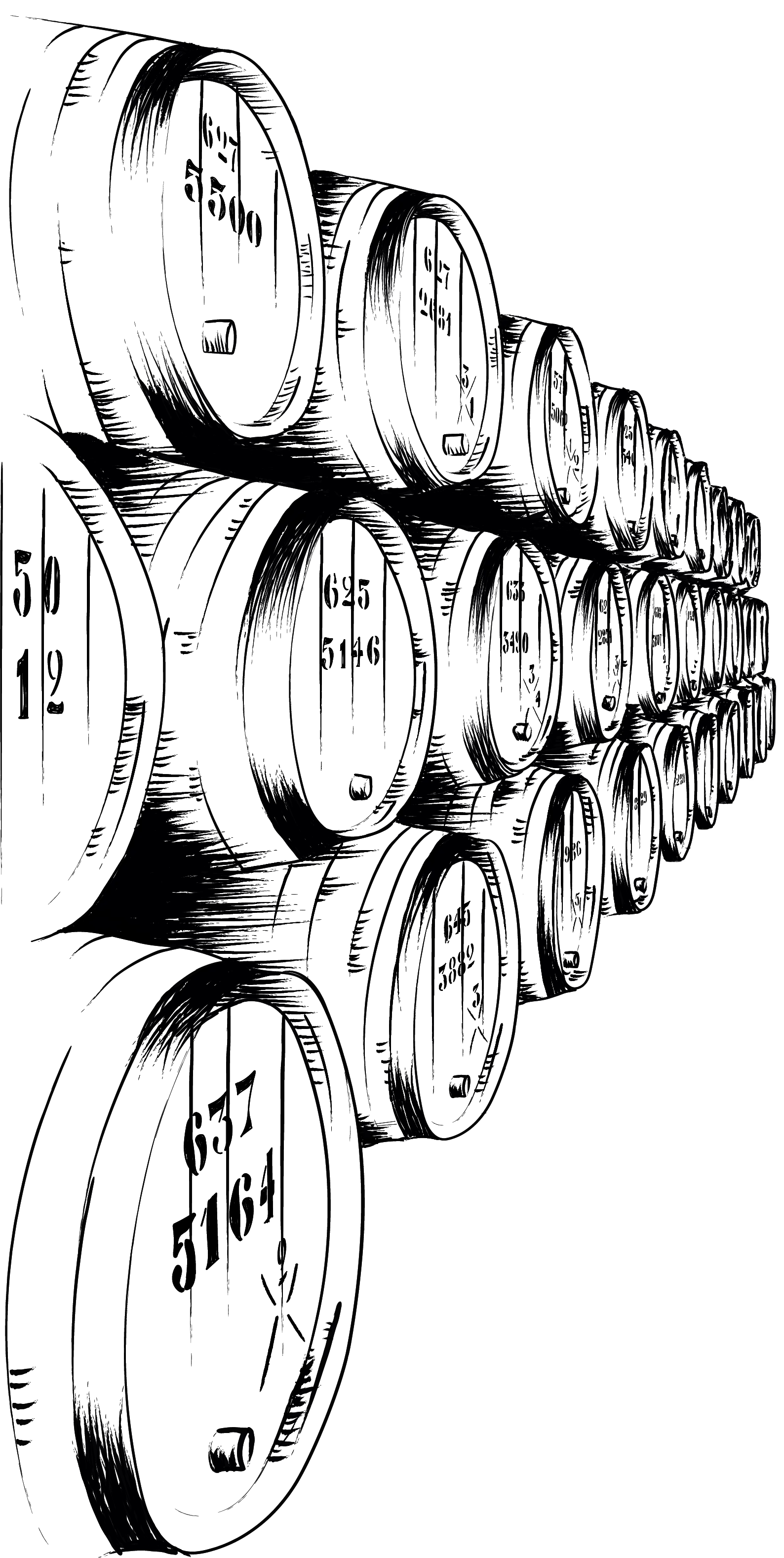
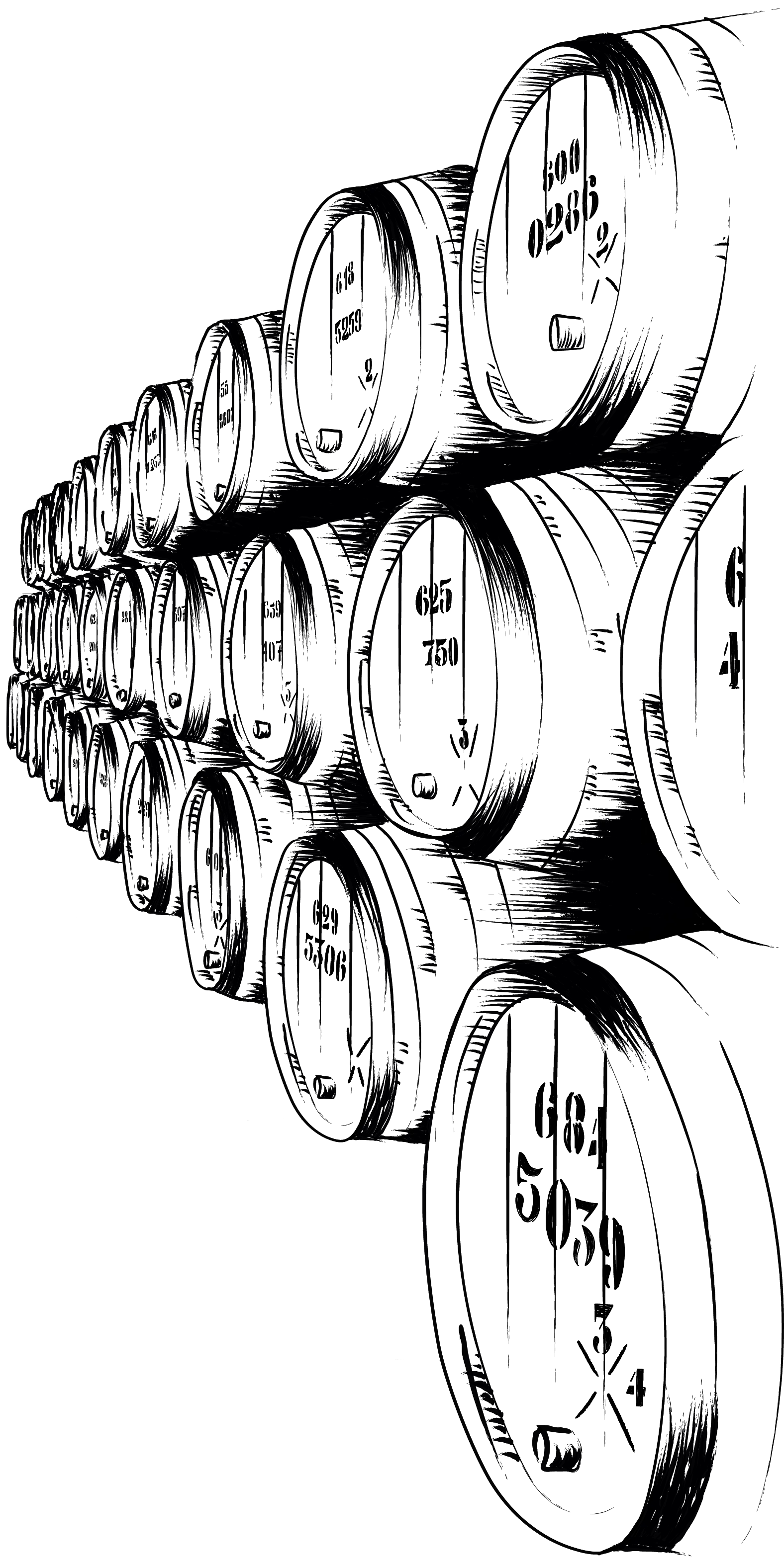
discover more